
PROCESO SIDERÚRGICO
El primer paso es introducir el mineral de hierro en el alto horno junto con los fundentes, que suelen ser rocas calizas.
En el alto horno se usa un carbón especial llamado coque.
La coquización consiste en la destilación del carbón en ausencia de oxígeno. El proceso de coquización comienza con el transporte del carbón desde la playa de minerales hasta los molinos para conseguir el tamaño adecuado. Los distintos tipos de carbón se almacenan en silos donde se mezclan para lograr la mezcla requerida. La conversión se realiza en hornos llegando a temperaturas de 1300 ºC. Cuando se eleva la temperatura, a 350º C aproximadamente, el carbón pierde su estado sólido para reblandecerse, formando una masa viscosa que permite la unión de sus moléculas y la posterior solidificación, lo que hace que el carbón pierda gran contenido de volátiles, para aumentar la concentración del carbono fijo, dando lo que se denomina coque.Posteriormente se realiza la descarga del coque, por medio de un pistón de descarga que atraviesa longitudinalmente todo el volumen del horno, derivándolo (a una temperatura de 1000º C en promedio) a un vagón de apagado, sobre el cual se descarga agua para enfriarlo. El tiempo de apagado es de 60 segundos por vagón. La operación de secado se completa con el calor residual. Luego, el coque se destina a una planta de Cribado, donde se realiza una clasificación por tamaño, para su posterior uso en el Alto Horno.
El alto horno es un horno vertical, alto, ensanchado en el vientre, cuyo objetivo principal es producir arrabio líquido.
El arrabio se produce en el Alto Horno y está compuesto por:
Hierro con un contenido de Carbono de aproximadamente 4% a 4,6% y otros componentes de impurezas tales como: Azufre (proviene fundamentalmente de la ceniza del coque, de la ganga del mineral de hierro y de los fundentes) Fósforo (proviene del mineral de hierro) Silicio (proviene de la ganga y de la ceniza de coque) y Manganeso (proviene del mineral de manganeso que se le carga al Horno).
El proceso comienza con la carga del Alto Horno. Esta se realiza con dos carros que llevan las materias primas hasta la parte superior (boca del Alto Horno). Por medio de toberas se inyecta al horno aire a 1150º C que, en su interior y en contacto con el coque, forma el monóxido de carbono (CO), el cual en su ascenso a través de la carga, le quita el oxígeno al mineral (fenómeno de reducción) formando gas dióxido de carbono (CO2) que sale por el tope. No todo el gas monóxido se trasforma en gas dióxido de carbono, sólo un 50%.
El oxígeno y el coque producen el calor necesario para que el mineral de hierro se funda, favorecido por la alta convección provocada por el movimiento de los gases. El funcionamiento del Alto Horno es continuo, pero la carga y la colada se realizan en forma intermitente. Una vez fundido los componentes, estas se drenan del alto horno por dos lugares: uno superior donde extraemos la escoria, llamado escoriero; y otro inferior llamado piquera donde se vuelca el arrabio. El trasladado del arrabio hacia la Acería se realiza en vagones que están especialmente diseñados (con materiales refractarios) para mantener y resistir las altas temperaturas (torpedos).
En la Acería se convierte el arrabio en acero, mediante una serie de procesos que cumplen la función de calentar y ajustar la composición de los elementos que contiene.
El convertidfor LD está formado por en una olla de acero recubierta en su interior con material refractario en la que se deposita el arrabio a tratar. A través de una lanza situada en la parte superior se inyecta oxígeno al recipiente. Debido a las altas temperaturas de trabajo, la lanza se enfría continuamente a través de serpentines de agua interiores para evitar que se funda. La carga y la descarga de la olla se hacen por la parte superior por lo que la olla está montada en ejes rotatorios que permiten su volcado.
Cuando el horno se ha cargado de arrabio procedente del torpedo y con chatarra seleccionada se coloca en posición vertical, se hace descender en su interior la lanza de oxígeno hasta unos 2 m por encima de la carga. A continuación se inyectan en el horno gran cantidad de oxígeno a elevada presión. El oxígeno reacciona con el carbono y otros elementos no deseados e inicia una reacción que quema con rapidez las impurezas del arrabio produciendo una escoria. Esta, al tener menor densidad, se sitúa en la parte superficial.
Normalmente el chorro de oxígeno contiene polvo de piedra caliza que sirve para eliminar impurezas, entre las que destaca el fósforo.
Terminado el proceso se inclina el horno para extraer la escoria, quedando abajo el acero afinado.
Una vez obtenido el acero afinado, se le pueden añadir los elementos que formarán las distintas ferroaleaciones, o bien hacerlo más tarde cuando el acero afinado sea vertido en la cuchara. El proceso tarda unos 50 minutos, y estos sistema están dimensionados para poder producir unas 275 toneladas de acero por hornada.
Una de las grandes ventajas que desde un principio se observó en estos convertidores fue su capacidad para aceptar hasta un 20% de "chatarra junto con la carga de arrabio líquido.
Después el acero es cortado adecuadamente para su uso.
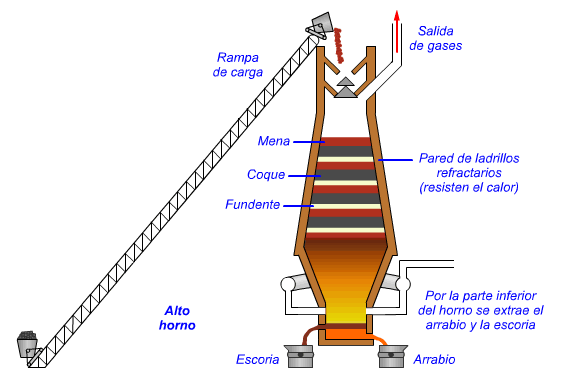
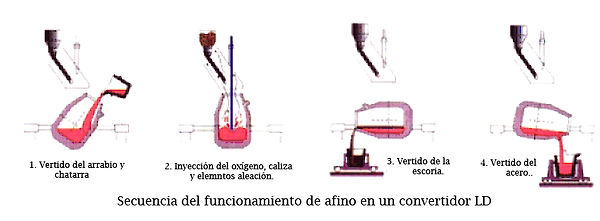